What Is Root Cause Analysis?
The FDA’s announcement in July 2020 about the new food safety norms includes adopting quality tools to ensure better traceability in the food supply chains. One of the quality tools recommended was the root cause analysis method, which allows the manufacturers to determine the source of the problem.
Root cause analysis (RCA) is used in the food supply industry and across sectors as a problem-solving mechanism. Identifying the source helps them to overcome it and ensure better safety norms. Here is the information on what RCA is and how to use the tool.
What Is RCA?
Imagine you have a broken wrist. It hurts, and you could take painkillers to reduce the pain, but that does not solve your problem. You will need treatment to fix the wrist bone for a permanent solution.
Similarly, when there is a problem, no matter the industry, you can look at the situation and consider multiple ways to fix it, requiring repeated attempts over time. Or, you can take a moment to get to the root cause of the problem to ensure that you provide a permanent fix.
The case could be human, machine, or mechanism related. It could also be related to any aspect of production, healthcare, operations, supply chain, transportation, telecommunication, or manufacturing. The root cause analysis method helps you trace the problem step-by-step, identify the stages where the issue started, and find the solution to overcome the concern. Several techniques can carry out an RCA, such as FMEA, Ishikawa diagram, Fault tree analysis, and Pareto analysis.
How to Use RCA?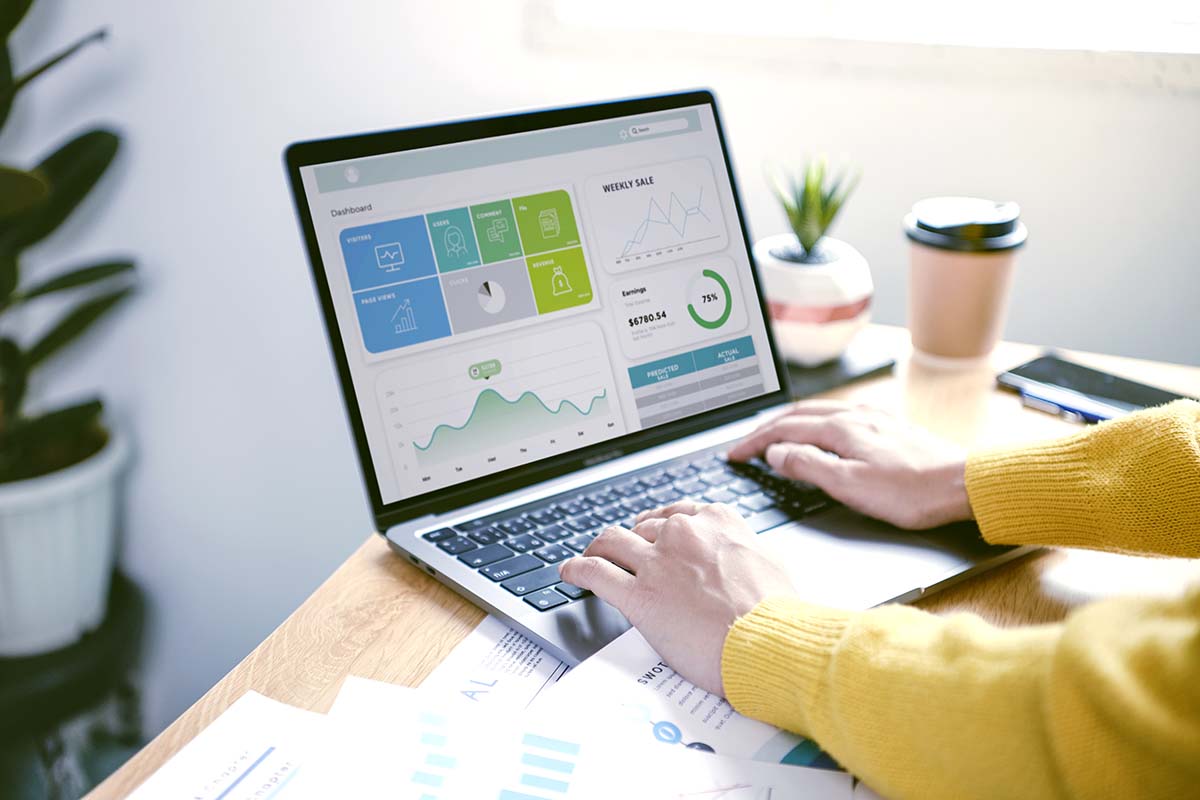
No matter which technique you use, the principle of the tool remains the same. It uses the four steps:
- Identifying and describing
- chronology
- differentiation
- casual graphing
You can use it to identify the problem, describe it, establish a timeline from the start of the process to the point of the problem, find the cause of the problem, and determine the events correlated to the problem.
What are the Challenges in Using RCA?
One of the quality tool’s challenges is the lack of data. This could be missing information, too much irrelevant information engulfing the relevant facts, and more than one cause of the problem. All data should be present to study a problem to create a thorough analysis.
Another challenge that the root cause analysis method faces is that the simple graphs may have many levels. The investigator usually terminates them at the level they consider the root. At the same time, there may be a more profound underlying factor.
Due to these factors, it can be challenging to design a robust RCA that helps identify the fundamental problem of these factors. Despite these challenges, the technique is a widely used quality measure across industries.
The method is a versatile quality management tool that can be used in any situation. It requires common sense and good judgment to identify the problem and its causes. It is a reactive process of quality control that helps organizations find the reason for a problem and fix it to ensure it does not repeat.